Targeting Embodied Carbon
Energy efficiency and operational carbon are key elements of eco-friendly building design, but the spotlight is increasingly turning to embodied carbon emissions as a critical factor in sustainable architecture.
In measuring the embodied carbon in building products, including glass, the accepted metric is Global Warming Potential (GWP), which is kilograms of equivalent carbon dioxide referred to as CO2-eq.
A variable that impacts the embodied carbon from the insulated glazing aspect of the glass-making process is the applied heat treatment. In addition, there are the materials and energy consumption used for lamination, coatings and insulating glass unit (IGU) production components including the spacer, sealant and desiccant.
Breaking out the embodied carbon in a typical IGU, 78% comes from uncoated glass production, 10% is attributed to the heat treatment and low-emissivity (low-e) coatings and 12% is accounted for in the IGU fabrication process.
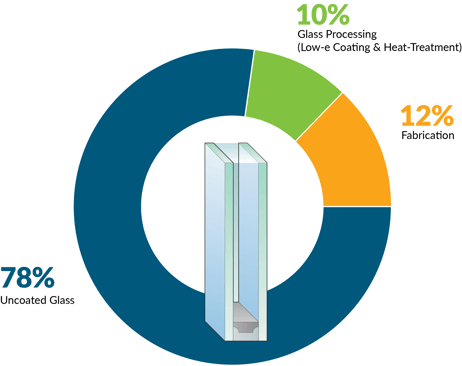
Carbon Reduction Strategies
To bring these embodied carbon values down, a number of strategies can be employed, both directly for the glass manufacturing processes and indirectly with plant operation improvements.
Perhaps most significant is the increased use of recycled cullet. Because there can be impurities and contaminants contained in recycled glass, flat glass manufacturers only accept cullet from known sources like their own customers. Otherwise, elements like nickel and aluminum can damage the glass manufacturing furnace and cause breakage in the final product.
The reprocessing and reutilization of cullet can account for greater than 20% of the new glass product and can significantly contribute to reductions in waste, energy consumption and raw material acquisition.
Another effective strategy is the use of Oxy Fuel technology. Whereas most furnaces mix preheated air with natural gas, oxy fuel utilizes pure oxygen to mix with the natural gas to produce higher flame temperatures. The result is a more efficient combustion process, reducing energy consumption in glass melting furnaces by as much as 20% and cutting greenhouse gas emissions in half.
Ways to decrease energy use through the glass manufacturing process include burner design and nozzle selection. To reduce power consumption in the plant facility itself, some energy- and resource-efficient building design strategies are variable frequency drives, LED lighting, building controls and low-flow fixtures.
Glass manufacturers can also investigate options to purchase power from sources known to use renewable energy.
Whole Building Perspective
To better understand and evaluate carbon, it’s important to view carbon through the full life cycle and whole building lenses.
A whole building perspective takes into account the significant reduction in operational carbon through the HVAC and lighting energy savings enabled by high-performance glass.
Meanwhile, by investing in IGU durability and longevity, this stretches the resources used to manufacture the unit, thereby preserving the carbon investment made in the flat glass. For example, by increasing the longevity of the gaskets and seals inside IGUs, service life can be extended.
In considering IGUs within the context of curtainwall/storefront and façade systems, whenever a design layers materials for the sake of aesthetics, this comes along with a higher embodied carbon price tag. For instance, a façade with a decorative rainscreen or glass sandwiched by a shadow box and sheet of metal may deliver a “wow” effect but can significantly drive up embodied carbon.
While beyond the scope of this glass-focused article, some aluminum and framing strategies for reducing carbon include considering alternative facing and lining materials, sourcing low-carbon aluminum and specifying longer-lasting finishes.
Calculating Carbon
Helping architects calculate emissions for different glass designs and applications, the Vitro emissions™ Carbon & Energy Calculator is an important tool.
By inputting key parameters including building type, location, orientation, window to wall ratio, shading and curtainwall performance, designers can compare operational carbon and embodied carbon numbers, and calculate embodied carbon payback.
For example, a new office building in Chicago with a 30% window to wall ratio, moderate performing shading and a moderate performing thermally-broken curtain wall takes 81 tons of CO2-eq embodied carbon for clear + clear glazing and 674 tons of CO2-eq annual operational carbon emissions.
If Solarban® 60 clear + clear or Solarban® 60 Starphire® + Starphire® glass is used, the embodied carbon increases to 111 T CO2-eq, and the CO2 is offset within 16 months after which time operation carbon savings continue to accrue.
Another industry tool is Building Transparency’s Embodied Carbon in Construction EC3 Calculator. The calculator takes input from glass and framing Environmental Product Declarations (EPDs) and produces GWP estimates.
Currently, the tool requests the construction details and performance criteria for systems like windows, doors and skylights to calculate GHG emission numbers. This includes variables like the number and thickness of the glass lites, assembly U-value and solar heat gain coefficient (SHGC), the type of thermal separation in the frame, glass coatings and service life.
To help refine the glass and fenestration aspect of the calculator, Vitro, along with industry partners like the NGA and the Fenestration and Glazing Industry Alliance, are part of the development team. Currently on the docket is better defining applications for things like substrates, coatings and fire-rated glass to better identify similar products and the ability to compare apples to apples, so to speak.
Environmental Product Declarations
As architects research the products best suited to help them achieve their projects’ sustainability goals, Environmental Product Declarations (EPDs) are another very useful tool that can be used to demonstrate a product’s compliance with legislation and standards codes. An EPD is a detailed, third-party certified report of the energy use and emissions surrounding the manufacturing of a product—in addition to the packaging extraction, transportation and processing of related raw materials.
Codes and Legislation
Moving forward, embodied carbon emissions will continue to be a hot-button issue, particularly with increasing initiatives and legislation reducing carbon in materials used for building projects.
For example, as the largest purchaser in the world, the U.S. Federal Government’s Federal Buy Clean Initiative was established to promote the use and development of low-carbon, made in America construction materials.
Following up on this action, the General Services Administration (GSA) announced in 2024 that it has set standards for products that can be considered low embodied carbon (LEC). As part of achieving these standards, products must offer a Type III Environmental Product Declaration (EPD) with a Global Warming Potential (GWP) in kilograms of carbon equivalent per metric ton (kgCO2eq/ton) of glass. Products may fall into one of three set limits of embodied carbon:
- Acceptable: < 1,401 kg CO2 eq.
- Preferred: < 1,370 kg CO2 eq.
- Most Preferred: < 1,331 kg CO2 eq.
In 2024, Vitro updated its third-party verified Environmental Product Declarations (EPDs) to indicate its architectural glass products contain just 1,240 kilograms of CO2 equivalent, which is 13% lower than the National Glass Association’s industry standard.
Based on these results, all Vitro Architectural Glass products meet the Top 20% ("Most Preferred") Low Embodied Carbon (LEC) material category based on standards set by the Inflation Reduction Act of 2022 and the U.S. General Services Administration (GSA). This lowest embodied carbon designation applies to all Vitro-produced architectural glass from all Vitro plants all the time.
Glass is one of four building products for which the GSA has leveled LEC standards, and while other types of products may need to sacrifice quality in order to achieve LEC status, the composition, characteristics, clarity and strength of glass can remain the same because most carbon reduction strategies currently in place have to do with optimizing manufacturing efficiency rather than changing the formula of the glass product itself.
On the state level, California is leading the way in embodied carbon legislation. The Buy Clean California Act requires building projects to procure some low-carbon materials the California Carbon Intensity of Construction and Building Materials Act directs the development of a framework for measuring and reducing the average carbon intensity of building materials targeting a 40% reduction by 2035.
In addition, changes to CalGreen, the state’s green building code, includes mandatory embodied carbon provisions for large commercial buildings and schools.
Other states with embodied carbon-related procurement policies include Colorado, Connecticut, Minnesota, New Jersey, New York, Oregon and Washington.
For information about Vitro’s commitment to sustainable products and practices, please visit vitroglazings.com/sustainability. For any other glass questions, please contact Vitro Glass or call 1-855-VTRO-GLS (1-855-887-6457).
Updated on July 22, 2025